This past Monday night in my Intermediate Wheelthrowing class, we discussed how to throw with a bit more “intention”… and how to approach throwing “matching sets.” I offered up a few options… as one of their class challenges is to bring two “matching” bowls to our final class as few weeks from now! One of my best suggestions is to throw a few extras that are “similar” and then decorate & trim them to make them match even more… and then pick the two that match the best!!! I went with four… hoping to get two that match!!!
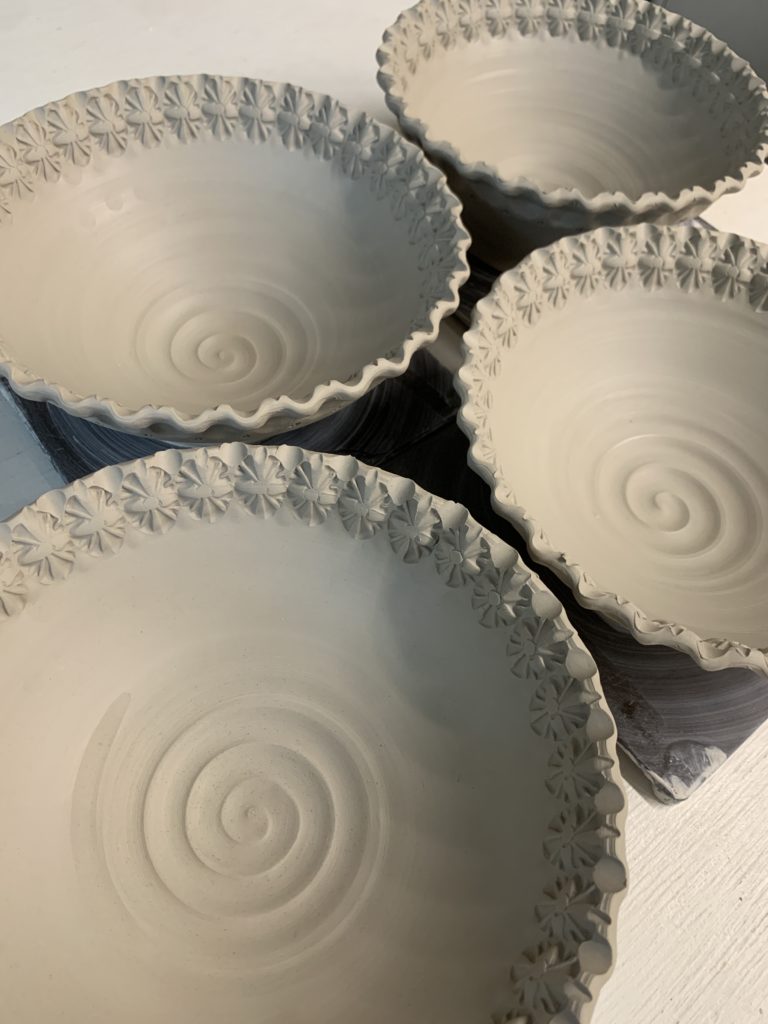