And while I was already throwing off-the-hump… I decided I should make another batch of mini’s while I was at it. I mean, who doesn’t want more cutie-patooties?!
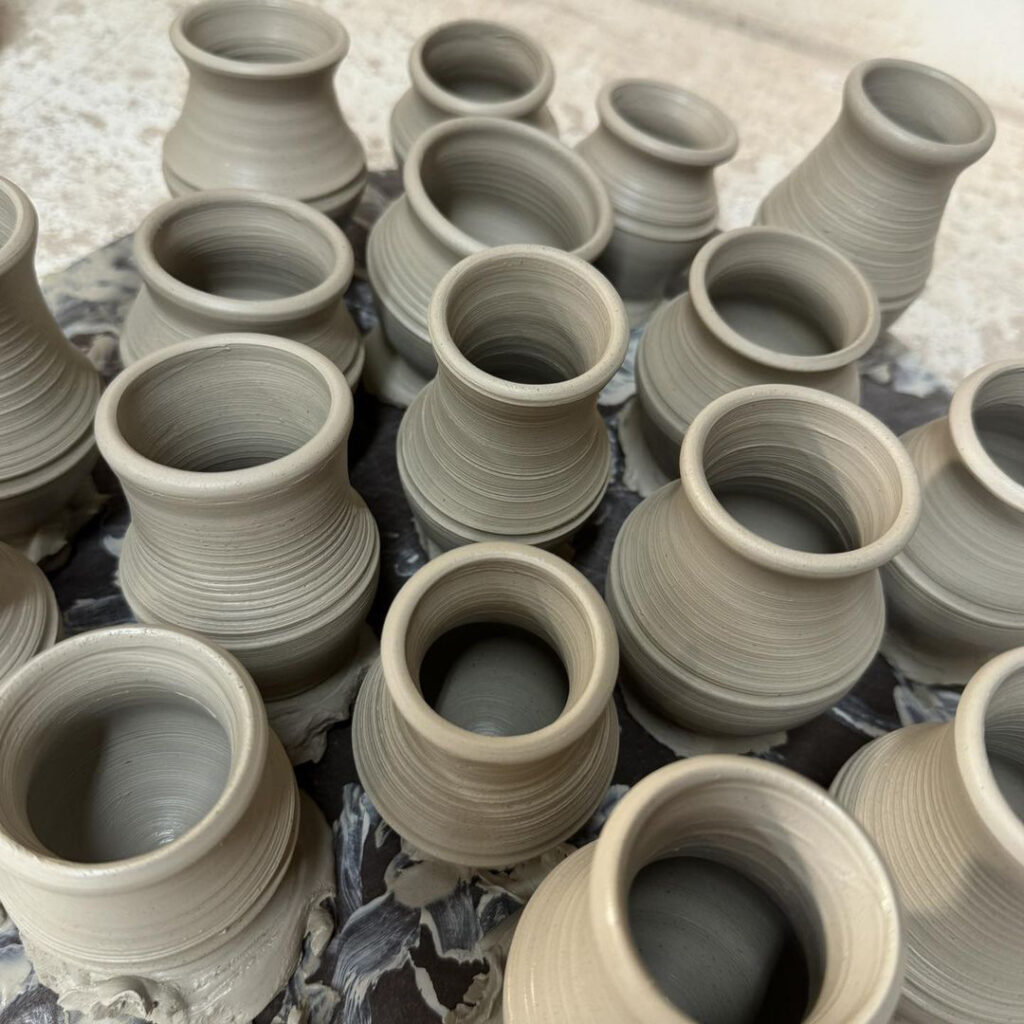
Gary Jackson: Fire When Ready Pottery
A Chicago potter’s somewhat slanted view of clay & play |
And while I was already throwing off-the-hump… I decided I should make another batch of mini’s while I was at it. I mean, who doesn’t want more cutie-patooties?!
So a customer contacted me just to ask if I would have ornaments again this year… the “top-shaped ones”! Of course I said “Yes”… but then realized I probably should make more before I commit?! So I did… another 10×10 Challenge! More than ten by 10:00am! Another productive morning!
Another Monday for making more mugs!!! Yep, after a busy weekend at ART IN THE GARDEN… there’s no rest for the weary! Gotta make more… more… more! I have another soda kiln to fill in a week and a half… yikes! Making more stuff for ART IN THE BARN!!!
Kinda diggin’ this early morning production thing! Cranking out some flower pots early this morning… before heading back outside to play this afternoon! Gotta get these moving… as ART IN THE GARDEN is now just two weeks away!
A very productive morning in the studio before 10am… cranking out another batch of mugs! Starting with a bagful of clay… and voila’… twenty mug cylinders!!! Lots of stamping to come!
Just finished another week of Wheelthrowing Summer Camp… and they cranked out a ton of cool pieces this week! All trimmed & decorated with colored slips. Now just waiting to be bisqued, clear glazed & fired again. Not too shabby for a bunch of 10-11 year olds, right?!
Another early morning being productive in the studio… making more than 10 before 10:00am!!! Now I just have a lot of “detailing” to make them come to life!!!
Making mugs again… but this time they’re part of the class challenge I gave my Intermediate Wheel students. They’re all working on sets of four MATCHING MUGS for our final class of the session! So I’ve got to step it up and make mine too! As I told them, I would never “stress out” over making just four that match perfectly… measuring, refining, stressing. Instead I’m making a lot of cylinders that are very similar, and then I’ll pick out the closest “matching” ones later!
A roomful of summer campers making a LOT of pots! Not bad for three days of wheelthrowing, one day trimming & one day painting. They were busy little campers this week… especially for a four-hour camp!!!
Now they’re off to a bisque firing, then a clear glaze & another firing to finish them off. And then the kids will come back to pick-up their pottery!
As if Wheelthrowing Summer Camp weren’t fun enough… I challenged my pre-teen campers to do a little blindfolded throwing!!! And they LOVED it!!! After just two-and-a-half days of learning to throw on a pottery wheel, I think they did an AMAZING JOB… and the giggles were absolutely contagious!!!
Gary Jackson: Fire When Ready Pottery
Lillstreet Studios ∙ 4401 North Ravenswood, Chicago, Illinois 60640 ∙ 773-307-8664 gary@firewhenreadypottery.com |